While the majority of Joplin’s lead and zinc mines were below ground, and in fact, much of Joplin is built above those shafts, there were some that were open to daylight. Below is a photograph of one of the best examples, the aptly named Daylight Mine.
A History of the Joplin Union Depot – Part III
Catch up on the history of the Joplin Depot’s origins with part one here and part two here.
After the exciting publication of an architect’s drawing of the Union Depot on the first day of March, 1910, a debate may have erupted over the validity of the print. The News Heraldon the 28th of March, in one of the first updates on the depot since the beginning of the month, confirmed the accuracy with the arrival of the official plans and specifications to the city engineer’s office. The city engineer, J.B. Hodgdon, passed on the plans to several local contractor firms. It was the hope that a local firm would offer a satisfactory bid, such as Dieter and Wenzel, located in nearby Carthage and a company responsible for raising many of Joplin’s most well known buildings. Notably, the city planned to divide the construction process between building the depot structure and grading the land about the building. The land in question, the Kansas City Bottoms, located between Main Street and the Kansas City Southern tracks and between Joplin Creek and Broadway, was to be leveled.
Two days later, the papers announced the appointment of E.F. Cameron as the local attorney for the Joplin Union Depot. The announcement was accompanied by a firm statement that construction would start April 1. In the meanwhile, the parties behind the depot had finalized the acquisition of properties within the desired realm of the depot and exploratory drilling had been done to ensure that no abandoned mines or “drifts” threatened to destabilize the foundation of the future depot. Indeed, the drilling had discovered solid limestone on average fifteen to twenty feet below the surface, and in some cases, even closer. Already, some of the uneven parts of the Kansas City Bottoms had been filled by the railroads to allow future track to be on level with existing rails.
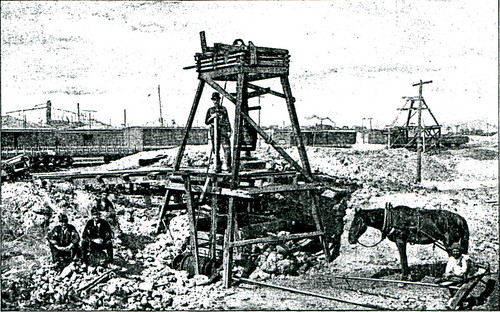
The site of the depot had once been the center of many mining attempts like the one above in the early days of Joplin, leaving many abandoned mines behind.
Six bids were submitted for the excavation, which required the removal of approximately 40,000 yards of dirt, and the Joplin firm Jennings & Jenkins was awarded the contract. “I will begin work,” declared W. F. Jenkins on Saturday, April 2, 1910, “with a full crew on the excavation on Monday.” Nine bids, two from Joplin area firms, were submitted for the construction of the depot structure. However, the selection of the firm was considered more important than excavation, and demanded a meeting of the chief engineers of the Missouri, Kansas & Texas, the Santa Fe, and the Missouri and Northern Arkansas, railroads. The architect, Louis Curtiss, available at the time of the bid announcement, promised that Joplin’s depot would be the most beautiful in construction, the most complete and convenient of any depot of the size in the United States. Indeed, Curtis noted, specifications called for “handsome interior furnishings and the most substantial exterior known.”
On the following Monday morning, a small force of men with three to four teams of horses arrived and began the work of excavation. The number of overall men expected to work varied from as little as fifty to four times that number, with as many four times the starting number of teams of horses. Afterward, it was reported that before rain brought an end to the day’s labor that fifty men with fifteen teams had been brought to bear against the earth.
The delay in selecting a contractor to build the depot structure was not critical, as all reports stated that such construction could not begin until the grading was complete. It was to be no small feat of work transforming the hilly area that offered a home to Joplin Creek into a suitable home for the new Joplin Depot. In contrast to the 40,000 yards of dirt discussed earlier, Jennings & Jenkins instead claimed they only had to remove 30,000 yards of soil. However, 135,000 yards of soil was required as fill, the present earth apparently being inappropriate for the task, and all of it to be hauled in by train.
The News Heraldsummarized the task ahead, “The hill along Broadway and Main street will be cut down and the dirt moved back onto the lower grounds. These hills will be cut down to a level of the grades of the streets and the fill along the Kansas City Southern railroad will be made on level with the tracks…The hill north of the Old Joplin creek bed will also be cut down and the dirt hauled into the low places.” Hills were not the only landmarks that needed cutting down, the paper referred almost in afterthought to, “Several buildings will have to be removed from the grounds during the next few days and a force of men will be set to work tearing them away and burning the rubbish.” The several buildings were actually homes to “persons who have occupied houses on the site for many years who repeatedly within the past month have been ordered to move.” No tolerance was given as the homes were to be destroyed as the excavation work approached them, not even “if the occupants have not sought other quarters.” The transformation of the Kansas City Bottoms was expected to take approximately two months.
Only a few days after the start of the work, the excavators made a gruesome discovery three feet into the soil of the hill located along Broadway. The Daily Globe reported, “The bones found are crumbled with age, and, although apparently whole when unearthed, fall to pieces when picked up; Their sizes are thought too large for small animals and too small for horses or cows, or other of the larger domestic beasts.” Work came to a temporary stop as local residents were quizzed for knowledge of any remembered burials or graveyards. None were recalled. One such resident, who claimed to have prospected “all over the Kansas City Bottoms when a young man” had never heard of any burials.
The old prospector reminisced, “They might have been buried all right,” said he, “but it was not with the knowledge of the authorities or a permit from the coroner. There was a killing down here almost every day in them times, and I suppose they had to bury the victims some way.” The reporter of the Daily Globe noted that the majority of murders in the Bottoms were likely never reported, and the speculation that the excavators had discovered one unfortunate victim was very likely, an opinion shared by the Joplin police called to the scene. However, the contractors “scoffed” at the idea, most likely out of fear of losing workers who, “showed unmistakable signs of nervousness when the discovery was made…Several declared they would not work if they were convinced they were digging up bones of human beings.” Human remains or not, the excavation continued.
Another problem arose at approximately the same time as the excavators made their unpleasant discovery. Nine bids had been submitted for the contract to build the depot structure and to the consternation of the railroads involved, all were considered too high. The possibility of revising Curtiss’ design for the depot and re-opening the bidding process was proposed on April 8th. Five days later, the decision was made to do so and bidding was opened again until the 18th. The new bids were based on changes to the original design, contractor Fred Dieter reported, changes that “will not in any way effect the exterior nor the general plans for the building,” but rather consisted of, “a few substitutions in material.”
By the time the bidding process was closed, only six bids had been made, down three from the previous nine. A. F. Rust, the chief engineer for the Kansas City Southern, promised that the new bids all appeared to be a much more satisfactory in estimated costs. A week, the chief engineer promised, was as long as it would take for the winning bid to be selected. Nearly two weeks later, on April 30th, an authoritative source promised that the winning bid would be announced in two days, in part to coincide with a meeting of the chief engineers of the four railroads which backed the union depot company. By May 12th, James Edson, the president of the Kansas City Southern on a long distance telephone interview with a News Herald reporter, had to dismiss rumors that the depot was to be relocated to a 15th Street location. In the same call, Edson declared that a meeting of the board of directors of the Joplin Depot Company in the later half of May would choose the winning contract. Meanwhile, excavation continued with dynamite used to reduce a steep hill east of Main Street.
Finally, on June 5, a Sunday morning, it was announced that the Manhattan Construction Company of New York, with a branch office in Fort Smith, Arkansas, had been awarded the contract at an initial cost of $60,000. Construction would begin, stated a representative for the company, no later than June 15. The grading by the excavators was virtually completed, but the foundation of the building had not yet been begun. The two city papers offered slightly different reports on the design of the building, the Herald claimed, “The trimmings will probably be of Carthage stone, according to the original plans,” along with brick and concrete, and the Daily Globe in turn stated, “The contract calls for the erection of a modern building, of reinforced concrete construction.”
Six days later, Rust visited the site of the future depot and promised again that the depot would be completed by the end of the year. The chief engineer noted that already enough steel for four miles of track was at the site and that, “We intend to push operations as fast as possible,” and bragged, “only material of the highest grade will be put in the depot. The station will be built with a view of accommodating Joplin when it is considerable larger than it is now. In my opinion, and according to officers of the depot company, Joplin is one of the coming cities of the Southwest.”
By mid June, excavation work uncovered yet another discovery, zinc. Within a week of the find, nearly a ton of the ore had been sold at a price of $23 a ton. While the contractors considered applying the new found source of wealth toward the cost of construction, two men from the excavation crew were assigned to sort the soil. The quality of the ore was shortly considered rich enough that some of the men involved in its examination immediately organized a mining company, procured a lease to do the mining, and set upon the deposit. The vein was found to be only a few feet beneath the soil, at least seven feet in depth, and in lieu of building a processing plant, the miners hauled away the dirt in wagons to nearby plants for processing to separate the zinc from the soil, as well any lead. By August 4, the entrepreneurs had sold nearly $1,900 worth of lead and zinc, and were still at work at their enterprise.
The excavated area, located “near the heart of the old shallow diggings on Joplin creek” had once been the home of St. James hotel and also the “crimson lighted district.” Old settlers, ever present to discuss such events, recalled the days when “the valley sloping off to the northeast resembled a bee hive. Mines and miners were constantly working there. Before many years had elapsed the ground looked like an overgrown pepper box.” However, due to the presence of the hotel and other sordid activities, few thought to mine the area, or so the theory went. The News Herald quipped, “If the owners of the new property do not see fit to construct their new depot they can mine.”
“Grading of site is nearly completed,” announced the Daily Globe, on June 16. By the efforts of the excavators, the paper reported that “the hills to the north have been leveled, while many of the lower points have been filled and the surface rolled.” Though, it took another four weeks to complete, the impact on the local geography was significant. In addition to the annihilation of hills, the “surface of the ground has been lowered seven feet…in the higher places, and from that to two feet in the lowest parts.” For the low parts of the depot area, fill was used to raise the surface from two to four feet. Extreme summer heat, contractors claimed, was the culprit for the long delay in the completion of the excavation. The teams of excavators gone, the site absent of working men and horses, for a brief time was considered to possess an “absolute quiet.”
A visit to the site at the time would have revealed a number of temporary buildings built to house the materials needed to construct the depot. The gathering of which had been ongoing for weeks. Another significant addition, and alteration to the geography, was the culvert built to guide the waters of the Joplin creek under the Depot site. When completed, the culvert was expected to be 631 feet long and possess a 6 foot radius. Through it the creek named for the Methodist preacher, Harris Joplin, would eventually disappear from sight for a stretch of more than two football fields. Nor was it the only effort to divert water, as a “great double aqueduct” was also being put into place to convey a stream from Main Street , built of concrete, it was two tubes each four feet in diameter and two hundred yards long. When done, it was believed the aqueducts would be able to “convey a larger amount of water than has ever been seen in the little branch.” The exit point for the aqueducts was in the area of the Kansas City southern bridge.
Off the site, at approximately the same time as excavation work was concluding, the Kansas City Southern filed a mortgage for the value of $500,000. The mortgage was intended to secure the $500,000 in bonds that had previously been sold by the depot company to finance construction. Nor was the Kansas City Southern the only railroad company involved with large sums of money. The Missouri, Kansas & Texas, or Katy, Railroad was busy with the construction of a spur from its main line to reach the Depot at a cost of around $250,000. Much of the cost had to do with traversing hollows and areas dotted with old mines and sludge ponds, which demanded the construction of bridges or the use of fill to stabilize the ground. One such required bridge was to be located over Possum Hollow and would be a “22-panel pile trestle bridge” that would carry trains 47 feet above the floor of the ravine, and 30 feet above an existing bridge built by the Frisco Railroad. Along with its own expense in the cost of terminals at the depot, it was estimated the Katy would ultimately spend $500,000.
While the Katy Railroad continued its investment into the depot, another railroad decided to investigate the possibility of joining the enterprise, the Frisco Railroad. As covered earlier, the Frisco Railroad, through its interests in Joplin, had furiously attempted to stop passage of the union depot franchise by the city’s council. However, almost two years had passed since its failed attempt and faced with a desire to expand its freight capabilities by the cheapest means necessary, the Frisco opted to further investigate the matter. While the Frisco had a depot in Joplin, it believed that if it could direct its passenger traffic to the union depot, it could then enlarge its freight capabilities at the existing depot. Despite reportedly being on of the largest landowners in the city of Joplin, the Frisco was having trouble parting Ralph Muir from the property he owned at the corner of 6th and Main Street, which it felt was needed were it to expand its passenger area. The vice-president of the railroad, Carl Gray, promised a decision would be had in a couple weeks. Ultimately, however, the Frisco did end up building a new depot, after it did finally acquired the coveted 6th Street and Main property.
Meanwhile, as work concluded on the main excavation, on July 24, 1910, the Joplin Daily Globe, noted in a small article, far from the headlines of the front page, that the Manhattan Construction Company “Will Start Erection of Depot Tomorrow.” Representatives of the company were to arrive on the 25th, along with a foreman, who’s task was to oversee approximately 25 men and the start of the foundation, which included the further excavation of fifty square feet for the new home of the depot’s heating apparatus. The depot itself was finally under construction.
The Age of Zinc: The Wright Lead & Zinc Company
The Wright Lead and Zinc Company of Chicago, Illinois, was one of hundreds of companies that sought shareholders to help finance its mining ventures in Joplin. The president of the company, Walter Sayler, was an ambitious Chicago lawyer. A.H. Wilson, treasurer, was partner in a large real estate company and John W. Wright, secretary, was a “mining expert.”
He, along with his fellow officers and directors of the company, sent out circular letters advertising the opportunity to purchase stock in the anticipation that the company would strike it rich in the lead and zinc mines of Southwest Missouri.
The company’s letter must have intrigued a few investors. The stock was said to be a “safe 12 per cent investment; a probable 3; a possible 48.”
The company owned over 500 acres of land divided between four properties. Wright Lead and Zinc planned to sink twenty shafts across its four properties, and expected to make an estimated $40,000 per month before payroll, royalties, material, and other costs, leaving a $20,000 profit.
In case one might have doubts about investing, the letter included a circular with endorsements from various politicians and businessmen, descriptions of Joplin and mining operations, and a selection of “Tales of Fortune.”
Joplin was described as “utterly unlike any other mining camp in the United States. It is a combination of the east and west, of the north and the south. It is at bottom an agricultural and commercial town, upon which has been superimposed a thick layer of American birth.”
It was in Joplin that one tenderfoot, along with his partner, was seemingly hoodwinked by two seasoned local miners when they purchased a piece of land long thought tapped out. But the two greenhorns, not knowing any better, worked their land and eventually struck a new vein of ore that allowed them to buy a new hoist and other mining equipment. Within a few months, they had cleared $33,000 in profits. Then there was the story of a young man from Kansas City who, with $150 in capital, began work on a modest claim. He found enough ore to build a mining plant which he then used to bring up $30,000 out of the mine.
Even Mrs. M.C. Allen, Joplin’s famous mining queen, was mentioned as one of the mining district’s success stories. Having failed to sell her land for $50 an acre, she leased it, and made a fortune. Intriguingly, after telling of Allen’s success, the circular added, “Among the mine operators of the district are several women, and almost without exception they have done well or have prospects of making large profits in the near future. Their lack of mining knowledge is more than offset by the gallantry of the land owners and promoters, who see to it that the ladies who so pluckily venture into mining are given the best locations and every assistance [sic] possible.”
As the circular noted, “One of the richest men in Joplin was once a bartender; another drove a brewery wagon; others labored in the mines or worked in stores or on farms, and had only their hands to work with. Riches came to the lucky ones.”
But the days of luck were over. Within a few decades the mines of Joplin would stand still, only to fade away, leavening behind faint memories of a proud mining history.
“Young Men Are Dying” – Frances Perkins’ visit to Joplin
On April 23, 1940, a crowd of two hundred people stood on the train platform at Joplin’s Frisco Depot, awaiting the arrival of an important visitor to the city. Many of them would have identified themselves as union representatives, but their visitor was not famed labor leader John L. Lewis, head of the United Mine Workers. Instead, when passengers began to disembark from the train, the individual who captured the crowd’s attention was a woman, often described by her contemporaries as “plain,” perhaps even ordinary looking. Plain and ordinary she was not. Frances Perkins, U.S. Secretary of Labor, was the first woman appointed to a position in the U.S. Cabinet. In response to the epidemic of “miner’s lung” in the Tri-State Mining District, Perkins convened a conference known as the Tri -State Silicosis Conference to allow concerned citizens, representatives from mining companies, government officials, and union representatives to discuss the issue.
Among those waiting at the platform to greet Perkins were Evan Just, secretary of the Tri-State Zinc and Lead Ore Producers Association; Frank Evans, president of the association; and the Reverend Cliff Titus, representing the Joplin Chamber of Commerce. Perkins then headed to the Connor Hotel where she stayed during the duration of the conference. She held a five minute press conference in which she stated that the purpose of her visit “is because you have silicosis there, and the labor department is concerned in preventing and correcting conditions due to silicosis.” After the press conference concluded, Secretary Perkins then headed outside to board a specially chartered bus. Together she and thirty other individuals representing various interests toured the mining district. Traveling out of Joplin on Route 66, she sat at the front of the bus with Tony McTeer, the district CIO president, and Evan Just. While driving past squalid miner’s shanties, Secretary Perkins remarked that something needed to be done to help those living in such dire circumstances.
The first stop was at the St. Louis Refining and Smelting Company’s Ballard Mine near Baxter Springs, Kansas. Secretary Perkins donned a “miner’s metal hat, raincoat, and overshoes” before she descended 350 feet into the mine where she then watched demonstrations of different mining methods. She was reportedly very interested in the “methods used by miners in drilling and in a dust control demonstration” given by Fred Netzeband, air hygiene engineer of the Tri-State Zinc and Lead Ore Producers Association. Secretary Perkins was later quoted by an observer as saying, “The world should know the true picture of methods being used in controlling and eliminating dust in the mines.”
After the demonstration, she then met with several of the miners, shook their hands, and listened to their views of the different methods used to control dust. Perkins was accompanied twenty other interested individuals, including Episcopal Bishop William Scarlett of St. Louis; the Reverend Charles Wilson of St. Mark’s Episcopal Church in St. Louis; and Miss Elizabeth Wade White of New York. All three were members of the Tri-State Survey Committee. It was perhaps the one and only time that a bishop of any religious denomination toured one of the Tri-State District’s mines.
Secretary Perkins then visited Treece, Kansas, and Hockerville and Picher, Oklahoma to view housing conditions. In Treece, she visited the home of Mr. and Mrs. William Hannon. Hannon and two other former miners told Perkins that they suffering from silicosis and were unable to receive treatment. Hannon’s wife and four children also reportedly suffered from silicosis. She then met with six women, described as the widows of miners, who stated that they and their children were plagued by silicosis. Secretary Perkins’ bus did not stop in Hockerville and Picher, but she was reportedly able to view “slum conditions” in all three towns from her bus seat. She then returned to the Connor Hotel and prepared for the conference which began at 2 o’clock in the afternoon. The conference itself was held on the roof of the Connor.
The conference revealed a variety of attitudes. After making her opening remarks, Secretary Perkins was followed by the Reverend Cliff Titus. Titus, appearing as a “representative of the public,” declared that workers in the Tri-State Mining District were all white, not foreigners; and that “they are independent and prefer to choose their own methods of living.” He then continued “Many of our people prefer to live near chat piles because they want to spend their money on other things” like cars. But Titus acknowledged that “people of the district are willing and anxious to bring about better living conditions in the mine sections and will co-operate with state and federal agencies.”
Evan Just, secretary of the Tri-State Zinc and Lead Ore Producers Association, spoke on behalf of a majority of mine operators. He declared that operators had made great strides in reducing silicosis over the last several years. Just cited statistics that allegedly showed that incidences of silicosis in miners had been reduced from 60 percent in 1913 to 22 percent in 1929. Further progress, he claimed, had been in the years since. What Just failed to mention, however, is that this only applied to the large mining companies who could afford modern mining equipment, and not the smaller independent operators who could not. Just, however, denied that individuals could contract silicosis from surface dust.

Miner shacks from the turn of the century - the condition of miners' homes continued to be poor decades later.
He then addressed living conditions in the Tri-State Mining District by stating that slum conditions were the result of social problems. “That many people who can afford better homes prefer to live in small, unpainted two and three-room shacks and spend their surplus funds on automobiles and radios cannot be charged against the mining industry,” Just maintained, although he claimed the mining industry did want to eliminate squalid living conditions. He was followed by representatives from federal and state public health, relief, and labor agencies. Even former Joplin resident Mrs. Emily Newell Blair, the noted political activist, was in attendance. Notably, former miner and the district CIO president, Tony McTeer, spoke in the interests of miners. He said, in part:
“Madam Secretary, ladies and gentlemen, conferences as such are not new to you, and to many people it is the usual approach to a problem, to sit down with all interested parties and discuss what is wrong in order to agree on a remedy. I can frankly tell you that a conference of this sort is new and different to the working people of the Tri-State area…
Some people believe that because the miners have not made a lot of noise about their troubles, because of the ignorance of themselves and others, that the workers have no troubles. That is not correct.
I am proud of our miners here. They know they have troubles aplenty, and what they are, but they also know false hopes when they see them. They have been fooled too often, so that now they don’t let themselves in for another deception.
However, they also know a good beginning when they see it. And this conference was received by the people of the Tri-State with great hope and anticipation of beneficial results…
We appreciate your coming this long distance, knowing that you would be convinced that here lies a serious problem.
Young men are dying. Ailing mothers and sick little children arouse in you the interest you have shown by being here today. Our district has the greatest percentage of widowhood in the United States; a sad commentary. These are the things that must be stopped for the future welfare of all the citizens who live here.
The problem as we see it is threefold. First, dust control; second, proper hospital facilities; third, adequate housing.
To reduce the high death rate among the miners requires better dust control and better working conditions in the mines. Stopping silicosis is one step in the direction of curbing the infection of tuberculosis. Mines today go in for more mechanical equipment, as we are living in a world of progress. I haven’t myself worked in a mine for the last five years, but the mining conditions and the health of the miners are my business. Our people working in the mines today give many exact reports of what does on in the mines.
It is said that wet drilling has solved the problem of dust control.
There have been two general fields of mining in this district. First, what we term the old country, which is the Joplin, Webb City area. Second, the Oklahoma and Kansas mining district. In the Joplin district the drilling was done with the piston machine or dry drills. The water liner drilling machine was introduced into Oklahoma and Kansas fields in 1916 or 1917, and from around that period it has been used exclusively. I wish to speak from my own experiences on this. I have never worked in mines except where water-lined drills were used, and I have silicosis, or dust on my lungs. We can produce the names of hundreds of men who have never worked except under wet drilling conditions, and we have buried a great many of them. I have prepared a list of some of those men who I know have died. I am turning it, with my statement, over to the chairman of this meeting.
Since wet drilling alone does not solve the problem, the problem still is dust control. We must get at the root of the problem…”
At the end of the conference, the Tri-State Survey Committee of New York sponsored a showing of “Men and Dust,” a short documentary film by noted photographer Sheldon Dick. Dick had journeyed to the Tri-State Mining District to illustrate the impact of silicosis on the lives of area miners and their families. It was Dick who famously dubbed Treece, Kansas’s Main Street as the “street of walking death.” An estimated one hundred people stayed to watch the film in the Connor Hotel’s Empire Room. Evan Just decried the sixteen and a half minute film as a “smear campaign” against the mining district and the companies that operated there.
After twelve hours, Secretary Perkins was scheduled to leave Joplin to return east. She announced that she would “appoint in the near future a committee of representatives of the three states to explore the possibilities of perfecting a ‘state compact agreement’ for coordinating the work of concerned authorities and agencies.”
Before leaving, she spoke to a crowd of 700 to 800 people at an open labor meeting sponsored by the International Union of Mine, Mill, and Smelter Workers and the American Federation of Labor. Her speech focused on the need to improve housing and living conditions in the mining district. After concluding her remarks, Secretary Perkins then left to catch her train.
As David Rosner and Gerald Markowitz point out in their book, Deadly Dust, the issue of silicosis faded away because of the lack of a strong labor movement to press for better working and living conditions, and the subsequent collapse of the mining industry in the Tri-State region. After the death of FDR, subsequent administrations had little concern for miner’s lung. But for a brief period of time, Joplin and the rest of mining district captured the attention of the nation
Sources:Joplin Globe Deadly Dust: Silicosis and the On-Going Struggle to Protect Workers’ Health by David Rosner and Gerald Markowitz “What You Really Want Is an Autopsy”: Frances Perkins and the U. S. Government Conference in Joplin, Missouri, 1940 http://historymatters.gmu.edu/d/128/
Perils of the Mines – Snapshot 1910
From the beginning, lead and zinc mining in the Joplin district was a dangerous means to make a living, and if lucky, a fortune, too. The year 1910 was considered a good one, respectively, when compared to 1909 when 51 miners lost their lives. In 1910, in contrast, only 32 miners were killed in the pursuit of the valuable ore. Every year, mine inspectors from the state toured the mines which surrounded Joplin to ensure compliance with mining laws and to note deaths and the causes behind them. In 1910, two inspectors toured 551 mines and 65 accidents. Here are the results and a snapshot of mining in Joplin in 1910.
In summary, the most dangerous element in a mine came from above. Of the combined deaths and serious injuries, falling mine roofs accounted for 27% of the victims. The next deadliest was the more obvious danger of explosives in the form of premature explosions, squib shot (involved in the dynamiting process), and to a degree, the foul air which was caused by failing to blow out the air in a mine following an explosion. Sadly, even entering and exiting a mine bore a certain amount of lethal danger, as our previous post on the unfortunate Number 52 noted.
Source: Joplin News Herald
Mining and Picher, OK
The plight of Picher, Oklahoma is well known to locals of the Four State area. Discounting the disastrous tornado that ripped through Picher not too long ago, the lead and zinc mining resulted in a dangerous contamination of the town. The mining in Picher arose from the mining in the Joplin area, after all, the town gains its name from one of Joplin’s earliest mining entrepreneurs, O.S. Picher. Recently, Wired magazine has written an article on the town.
Addititionally, here’s a streaming video link to a entertaining documentary about Picher today and the effects of its mining past. It’s worth watching if only for some video of the process of mining, the same process used in the Joplin area.